Shanghai ACM Semiconductor Equipment Co., Ltd. (hereinafter referred to as "ACM Shanghai") (Sci-Tech Innovation Board Stock Code: 688082), as a leading supplier of wafer process solutions for semiconductor front-end and advanced wafer-level packaging applications, today launched the Ultra C vac-p negative pressure cleaning equipment for fan-out panel-level packaging applications.
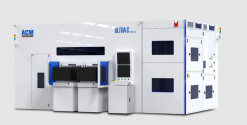
The equipment uses negative pressure technology to remove flux residues from chip structures, significantly improving cleaning efficiency - marking ACM Shanghai's successful entry into the high-growth fan-out panel-level packaging market. ACM Shanghai announced that a large Chinese semiconductor manufacturer has ordered Ultra C vac-p panel-level negative pressure cleaning equipment, which was delivered to the customer's factory in July.
“The emerging fan-out panel-level packaging approach is driving the growth of AI, data centers and autonomous vehicles, enabling increased computing power, reduced latency and greater bandwidth. This approach is quickly becoming a key solution that integrates multiple chips, passives and interconnects in a single package on a panel, providing greater flexibility, scalability and cost-effectiveness,” said Dr. Hui Wang, Chairman of ACM Shanghai. “The panel-level negative pressure cleaning equipment marks an important step for ACM Shanghai in solving the cleaning challenges of next-generation advanced packaging technologies, demonstrating continued innovation in semiconductor manufacturing and ACM Shanghai’s unwavering commitment to meeting evolving industry needs.”
According to Yole, the application growth rate of fan-out panel-level packaging methods is higher than the overall fan-out market growth rate, and its market share will increase from 2% in 2022 to 8% in 2028 compared with fan-out wafer-level packaging. The main driving force behind the expected growth is cost reduction. The utilization rate of traditional silicon wafers is less than 85%, while the utilization rate of panels is more than 95%. The effective area of 600x600 mm panels is 5.7 times that of 300 mm traditional silicon wafers. The overall cost of panels is expected to be reduced by 66%.
1 The improvement in area utilization has brought higher production capacity, greater flexibility in AI chip design, and significant cost reduction.
Removing flux residues before bottom filling is a key step in eliminating bottom filling gaps in advanced packaging processes. Due to surface tension and limited liquid penetration, traditional cleaning methods have difficulty in dealing with small bump pitches (less than 40 microns) and large-sized chips. Negative pressure cleaning allows the cleaning liquid to reach narrow gaps, thereby effectively solving this problem.
In addition, due to the long distance the liquid passes, traditional methods may not meet the cleaning needs of larger chip units. After using the negative pressure cleaning function equipment, the entire chip unit and even the central part can be thoroughly cleaned, effectively preventing residues from affecting device performance.
The Ultra C vac-p panel-level negative pressure cleaning equipment is designed for panels, which can be organic or glass. The equipment can handle panels of 510x515 mm and 600x600 mm and panel warpage of up to 7 mm.