Naura is developing an high volume Ion Beam Etching and a electron beam generators to improve the etching process for China next gen transistors and nanodevices
Electron beam generator and ion beam etching apparatus
Abstract
The invention provides an electron beam generator and an ion beam etching device, wherein the electron beam generator comprises: an electron beam generating cavity having an exit port; the shielding component is movably arranged outside the electron beam generating cavity; the shielding assembly is arranged to shield the outlet, and the outlet area of the outlet can be adjusted by adjusting the position of the shielding assembly. According to the scheme, the extraction area of the extraction opening can be adjusted through the shielding assembly according to the magnitude of the plasma density amplitude in the electron beam generation cavity, so that the extraction area can be adapted to the morphological change of the plasma sheath, the electron extraction efficiency is always maintained at a larger amplitude, and the performance and the stability of the electron beam generator are effectively improved.
With the development of micro-nano processing technology, the requirements on etching technology are higher and higher. Currently, etching can be classified into wet etching and dry etching in principle. Dry etching mostly uses the rf coupling principle to generate plasma sources, including inductively coupled plasma (Inductively Coupled Plasma, ICP) and Capacitively coupled plasma (Capacitively CoupledPlasma, CCP), to perform the desired etching process using ions or radicals in the plasma source. Compared with wet etching, dry etching has high etching precision, high controllability and good anisotropism, and is attracting more and more attention.
For dry etching systems, an electron source has an important role in addition to the ion source. For example, for high vacuum (e.g., gas pressure less than 10) -5 Below Torr) etching system, the successful ignition of seed electrons is one of the difficulties affecting system stability. One of the methods for improving the starting stability of the radio frequency system is to increase the number of seed electrons; in addition, in an ion beam etching (ion beam etching) system, in order to reduce repulsive force between ions, improve uniformity of ion beam current, reduce charge accumulation on a wafer surface, and improve etching rate, a sufficient amount of electron beam current needs to be provided to neutralize the extracted ion beam before an etching process is performed. Both of the above aspects require electron beam current that provides high density, stable output.
Examples of the electron beam generator that generates an electron beam include an ICP electron beam generator, which is a high-performance electron beam generating device. Compared with other types of electron beam generators, the ICP electron beam generator has wide applicable process scene range and long service life. Thus, attention has been paid more and more recently. The principle of operation of the ICP electron beam generator is as follows: the plasma is generated by inductive coupling. Under the action of the space electric field, positive ions move to an ion collector (cathode) with negative potential, and electrons are extracted from the extraction port. The balance of these two processes maintains the stability of operation of the ICP electron beam generator.
However, the electron beam generator in the prior art has problems of low electron extraction performance and efficiency.
With the development of micro-nano processing technology, the requirements on etching technology are higher and higher. Currently, etching can be classified into wet etching and dry etching in principle. Dry etching mostly uses the rf coupling principle to generate plasma sources, including inductively coupled plasma (Inductively Coupled Plasma, ICP) and Capacitively coupled plasma (Capacitively CoupledPlasma, CCP), to perform the desired etching process using ions or radicals in the plasma source. Compared with wet etching, dry etching has high etching precision, high controllability and good anisotropism, and is attracting more and more attention.
For dry etching systems, an electron source has an important role in addition to the ion source. For example, for high vacuum (e.g., gas pressure less than 10) -5 Below Torr) etching system, the successful ignition of seed electrons is one of the difficulties affecting system stability. One of the methods for improving the starting stability of the radio frequency system is to increase the number of seed electrons; in addition, in an ion beam etching (ion beam etching) system, in order to reduce repulsive force between ions, improve uniformity of ion beam current, reduce charge accumulation on a wafer surface, and improve etching rate, a sufficient amount of electron beam current needs to be provided to neutralize the extracted ion beam before an etching process is performed. Both of the above aspects require electron beam current that provides high density, stable output.
Examples of the electron beam generator that generates an electron beam include an ICP electron beam generator, which is a high-performance electron beam generating device. Compared with other types of electron beam generators, the ICP electron beam generator has wide applicable process scene range and long service life. Thus, attention has been paid more and more recently. The principle of operation of the ICP electron beam generator is as follows: the plasma is generated by inductive coupling. Under the action of the space electric field, positive ions move to an ion collector (cathode) with negative potential, and electrons are extracted from the extraction port. The balance of these two processes maintains the stability of operation of the ICP electron beam generator.
However, the electron beam generator in the prior art has problems of low electron extraction performance and efficiency.
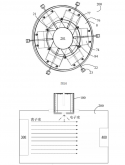