Software and hardware collaboration: Guangli Micro accelerates the whole process solution for improving the yield of integrated circuit manufacturing
Jiwei.com reported that Yield (Yield) is an important indicator of integrated circuit manufacturing, not only reflecting the technical value of the production line, but also a quantitative basis for continuous optimization of the process. Under the trend of shortage of production capacity, increasing the yield can directly increase the output value and reduce the manufacturing cost.
It is understood that the key to improving the yield rate lies in the effective monitoring and detection of the chip manufacturing process, and accurate and rapid analysis of massive monitoring data, identifying bottlenecks that limit the yield rate, preventing potential process risks in advance, and accelerating process upgrades and chip design optimization. .
Software and hardware synergy to create a yield ecology
In the wafer manufacturing process, it mainly includes process inspection methods such as physical inspection and electrical inspection. Wafer Acceptance Test (WAT for short) is the final electrical test for the quality control of the wafer when it leaves the factory. Through the test of the device and the test structure, relevant electrical parameters are obtained to characterize the process conditions and chip yield expectations.
It is understood that Guangliwei is one of the very few companies in China that can provide leading mass production electrical monitoring and yield improvement solutions, and has formed a "software and hardware synergy" yield ecology. The self-developed WAT testing machine has landed in the mass production lines and laboratories of several leading fabs, with EDA design tools, addressable (Addressable) and high-density (Dense Array) test chip technology, and DATAEXP data analysis platform Use to achieve design efficiency, effectiveness, and double the test speed. Through the standardized integration of the back-end production line database, a good data bridge and an effective closed-loop for yield feedback between upstream and downstream customers are established.
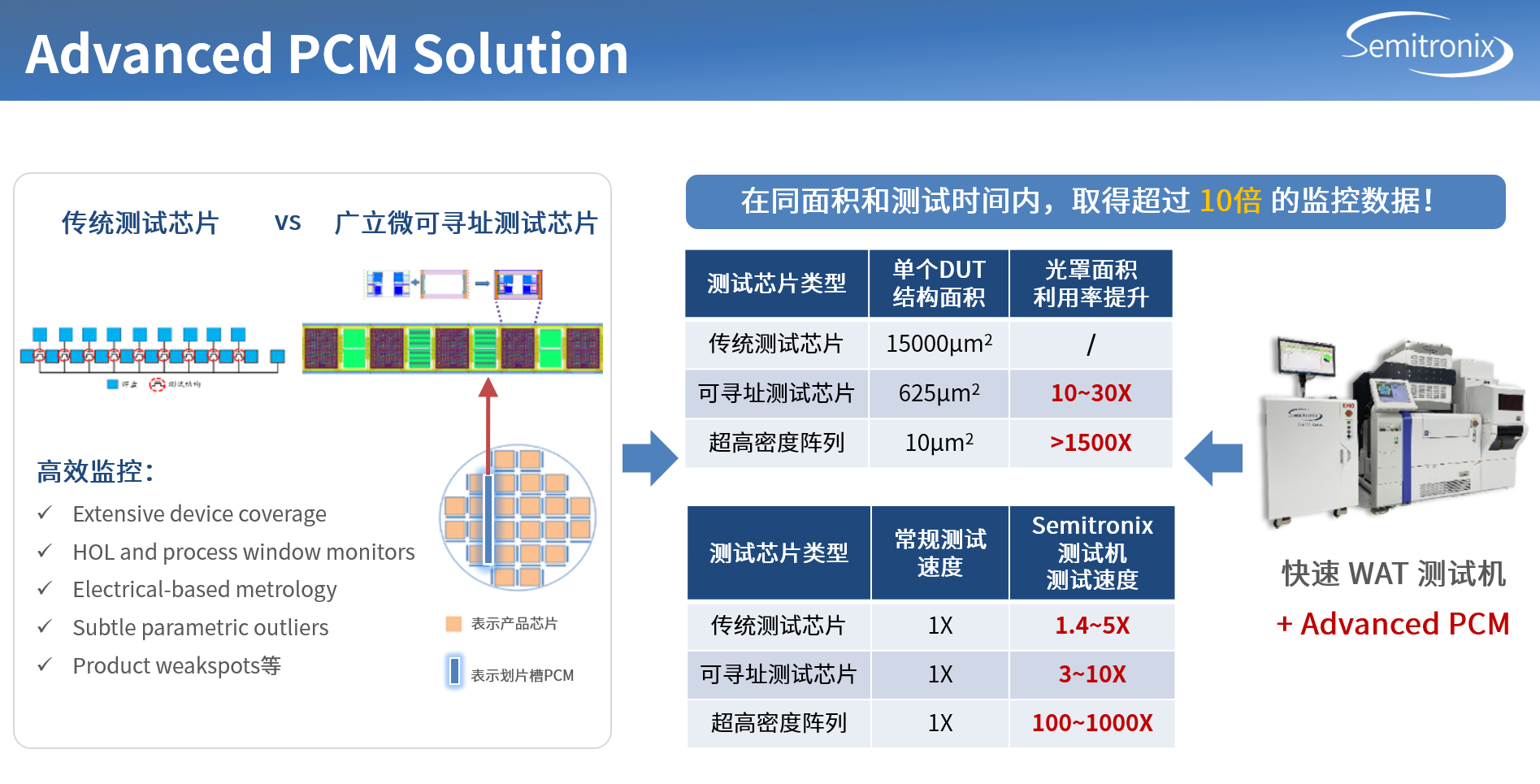
▲Software and hardware collaboration: quickly obtain more yield monitoring data
Guangliwei said, "Through the collaboration of software and hardware, our electrical monitoring solution can eliminate mines for the process development process, and the test efficiency can be increased by 10 to 1000 times. In addition, we also have a complete mass-produced electrical monitoring solution to ensure the stability of the domestic production line. It is understood that the company has recently developed an efficient mass production monitoring solution (Advanced PCM Solution) based on electrical testing, which can more accurately point to the root cause of yield failure during mass production.
Directly hit the pain points and shape all-round technical advantages
For electrical testing, test speed, cost, accuracy, comprehensiveness, and flexibility are all very important, but there are many difficulties in achieving efficient electrical testing, such as: accommodating more chips in a limited wafer area Test structure; improve design efficiency and design effectiveness through EDA software; improve test efficiency and control costs; realize data integration and analysis automation.
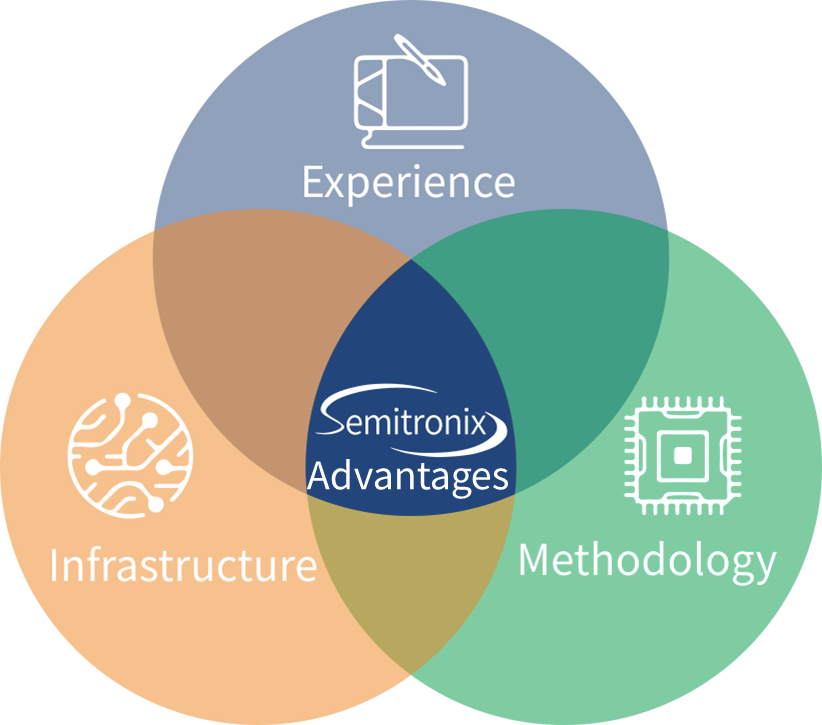
Guangliwei said that the company's Advanced PCM Solution covers a richer dimension of test content. In addition to the conventional yield monitoring structure, it has added related monitoring structures such as bottoming process windows, layout hotspots, device mismatches, and product sensitivity. Effectively conduct a comprehensive monitoring of the production line yield. High-density array technology can help chip design companies and fabs identify soft defects that affect yield at the ppm/ppb level (parts per million/parts per billion).
The traditional design scheme is limited by the number of pads, and the area utilization rate is low. However, Guangliwei adopts its own unique addressable technology, which can effectively improve the area utilization rate, increase the design unit density by 10-1500 times, and release more available area for dicing slots. The Advanced PCM Solution of Guangliwei achieves high-quality mass production through design and test collaboration; compared with traditional solutions, it reduces production costs, and in terms of yield monitoring and assurance, mass production line stability and predictability, etc., has obvious advantages.
Customized services to help fabs quickly achieve capacity expansion
In addition to technical advantages, Guangliwei also has a complete technical service team, which can tailor-made yield improvement programs based on specific needs of customers and provide diversified cooperation models. Guangliwei's partners already include: chip design companies (Fabless), wafer manufacturing plants (Fab), packaging plants (OSAT) and vertically integrated manufacturing companies (IDM).
Guangliwei said that the company has been formulating market strategies around the actual needs of customers and the technical pain points of the industry. Products and services that meet the needs of users.