800 million time and space ( Beijing Bayi Shikong LCD Technology Co.): The small-scale synthesis of the company's photoresist raw material PHS resin has been basically completed, and it is currently in heavy volume.
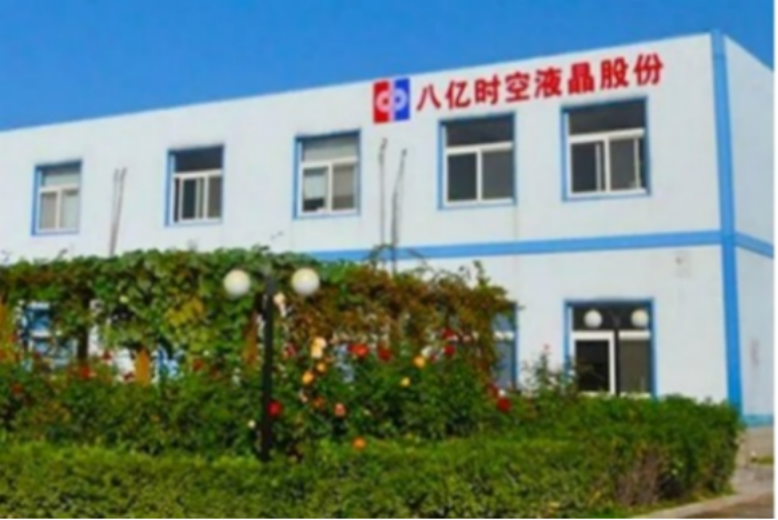
Jiwei.com reported recently, 800 million time and space said in an agency survey that the company has developed 12 new diamine and dianhydride monomers; PI slurry (MPI) has passed the small test tests of major manufacturers in the industry, and its performance indicators have basically reached international standards. At the peer level, preparations for the pilot test are currently underway.
In terms of photoresist, the company has ordered imported i-line and KrF248nm lithography machine and supporting equipment. The small-scale synthesis of photoresist raw material PHS resin has been basically completed, and it is currently in heavy volume. The semiconductor-grade PHS resin raw material for 248 nm has been optimized for the synthesis and purification pilot-scale process.