Scientific Hypotheses and Huawei’s Business Vision for the Future
Global Huawei Analyst Summit 2022
To reduce power consumption and improve reliability of semiconductor components, we are also working with researchers to explore the thermal mechanism in semiconductor components to see if we can create conditions to accelerate the conversion of optical phonons to acoustic phonons, reducing the temperatures of the gate electrode and drain of semiconductors.
Chip design
In chip design, most of the constraints on components are local. In this area, Georgia Institute of Technology researcher Peng Yang and his colleagues created an advanced algorithm with a computational complexity of the 2.3316 power of n. For this achievement, Peng won the 2021 Best Paper Award from SODA, a leading symposium on computational theories. A few months ago, our mathematicians created a revised algorithm, further reducing the complexity to the 2.28 power of n, 0.0516 power of nless than Peng’s algorithm. What does this improvement signify? It means that if nrepresents one million, our algorithm can further reduce the computational complexity by about 45%.
Based on these four pairs of hypotheses and visions, we have identified two scientific questions and eight technological challenges that we can work on together, focusing on innovations that fall in the Pasteur’s quadrant.
- How can we develop new processes that surpass complementary metal-oxide-semiconductor (CMOS) fabrication, cost less, and are more efficient?
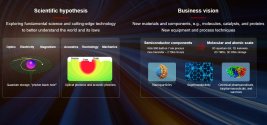
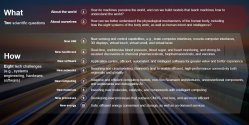