Dinglong Co., Ltd.: The third phase of Qianjiang polishing pad production line is in the trial production stage, and samples have been sent to mainstream customers for testing
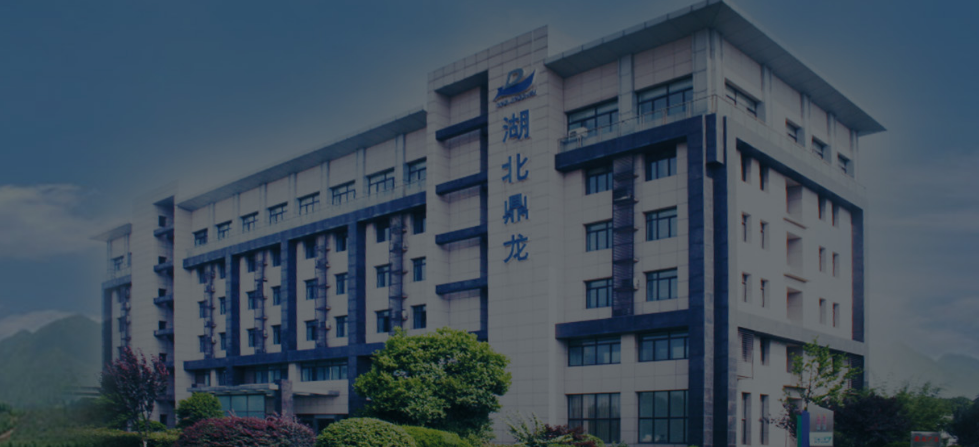
Jiweiwang news (text/Bai Yuxuan) On November 23, Dinglong shares said in an institutional survey that the total annual production scale of the first and second phases of the company's Wuhan headquarters CMP polishing pads is 300,000 pieces. In addition, the company's Qianjiang The industrial park has added 200,000 pieces of new polishing pads and 300,000 pieces of core supporting raw materials for expansion construction. Up to now, the new polishing pad production line of the third phase of Qianjiang project has been completed and is in the trial production stage, and samples have been sent to mainstream customers for testing. At present, customers have reported that the test results are good. In terms of market development, taking into account factors such as domestic demand for localization and overseas market promotion, the company reserves future production capacity in advance to ensure safe and stable supply.
It is understood that the core raw materials of CMP polishing fluid are mainly abrasive particles. At present, domestic raw materials are mainly imported from Japan and the United States. In the past, there was no way to localize abrasive particles, because the technical difficulty in this area was still very high. Dinglong Co., Ltd. started from the development of the core raw material abrasive particles upstream of the polishing liquid. At present, it has realized the independent preparation of three types of abrasive particles: ultra-pure silica sol, water glass silica sol, and alumina. The development of cerium oxide abrasive particles is also advancing as planned. middle. In terms of production capacity construction, there is a CMP polishing liquid production line with an annual output of 5,000 tons in Wuhan headquarters, and the capacity construction of the CMP polishing liquid expansion project with an annual output of 20,000 tons in Xiantao Industrial Park and the supporting expansion project for abrasive particles are being stepped up. Strive to complete the construction in the summer of next year, laying the foundation for the continuous and stable expansion in the later period.
Regarding wafer carriers, Dinglong shares said that the shortage of wafer carriers stems from two aspects. One is the demand for production expansion. Compared with wafers, the price of a single product of wafer carrier is not high, but it has a great impact on the yield rate of wafer mass production. Once a carrier supplier enters the fab, it will be particularly sticky to customers and difficult to replace. The difficulty of the carrier lies in the high precision requirement, which requires high mold design and injection molding process. The second is the difficulty of the production cycle and verification cycle. The largest mold currently developed by Dinglong Weibo weighs 15 tons and requires extremely high precision. In the process of customer verification, it is necessary to communicate with customers repeatedly from T0, and speed is also critical. Changhong is good at technology,
is the hardest 12-inch wafer carrier.
In addition, according to Dinglong, the proportion of the company's semiconductor material revenue to the company's total operating revenue has increased from 13% at the end of 21 to 20% in the first three quarters of 2022. The company's CMP polishing pad business is stable and improving. In addition, the company's various CMP polishing fluids, cleaning fluid products, and soft display materials YPI and PSPI products have been sold in batches and on a large scale. The company's semiconductor materials have entered a stage of rapid advancement. In the next two to three years, the company's revenue from semiconductor materials is expected to exceed the current revenue from printing and copying consumables.