Onboard integrated high-resolution microsatellite precision thermal control
In recent years, there has been an explosive development of micro satellites, and many high-performance micro optical remote sensing satellites have been launched. Integrated design of satellite platform and payload is a method to reduce weight and improve performance. rise of CCDs is less than 1 ℃/min during imaging. Firstly, the overall layout of the satellite is presented, the orbital heat flux under different conditions has been analyzed. Due to the fact that the - Z plate of the satellite faces the cold space, the - Z plate absorbs the minimum space heat flux and has the strongest heat dissipation capacity. Therefore, the bottom plate in - Zdirection is selected as the heat dissipation window for the entire satellite. Electronic components are designed reasonably to achieve temperature equalization. The maximum power of electronic components is 252 W. Reasonably set up heat dissipation channels to ensure that the temperature of electronic components will not be too high,which will affect its reliability and payload temperature stability. 0.01 ℃. And the temperature control of the secondary mirror is achieved through the use of radiation heating, which makes the temperature fluctuation of the mirror less than ±0.05 ℃. The thickness of the pyrolytic graphite sheets is 1.5 mm and its thermal conductivity is 900 W/(m·K). conductivity of 10 mm carbon fiber truss can be increased from 10 W/(m·K) to 126 W/(m·K) by using the 1.5 mm pyrolytic graphite sheets. In order to reduce the temperature changes of CCDs during imaging, phase change materials and thermal straps are used inside the satellite. Thermal straps can maintain thermal contact while allowing for positional changes of focal components. The thermal resistance of thermal straps is less than 1 ℃/W. When CCDs start working,heat is first transferred to the phase change material. Phase change materials absorb heat and melt, but the temperature remains relatively constant during the process, which reduces the temperature fluctuations of CCDs. After the CCDs work, heat is transferred out through thermal straps, and the phase change material solidifies again. Then, the finite element thermal analysis model is established and the simulation calculation is completed. According to the analysis results, the temperature gradient among the mirrors and the truss is less than 1 ℃, with temperature fluctuations within ±0.1 ℃. And the temperature of the avionics is within the required range,verifying the correctness of the thermal design. Finally, the thermal balance test of the satellite was carried out and the flight data of the thermal control system has also been collected. The results of thermal test and the in orbit temperature show that the temperature of the avionics ranges from 0 to 35 ℃, the temperature of the optical payload ranges from 19.5 to 20.5 ℃, and the temperature fluctuation is within ±0.05 ℃. The CCDs temperature ranges from 15 to 20 ℃, and the temperature rise during operation is less than 0.5 ℃/min, which meets the temperature control target and imaging requirements of the satellite, and verifies that the thermal design is reasonable and feasible.
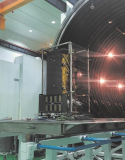