Hendrik_2000
Lieutenant General
China's first permanent magnet naval propulsion engine, designed by CSIC 712th, was successfully tested on a ship on October 18th.
I have no doubt it will find application in Submarine propulsion in conjunction with IEPS specially in submarine where space is at premium and having high efficiency over large load range is premium in Sub operation resulting in longer range specially if diesel fueled
PM machines have the ability to function efficiently at low speeds and throughout the entire load range. In vessels where all energy is produced by fuel, a lower consumption leads to an improved operational range and lower operational costs.
Here is the advantages of permanent motor over induction motor
PERMANENT MAGNET DRIVE TRAINS
THE SWITCH PMM 1000 M SHAFT GENERATOR
THE SWITCH ARGUMENT IS THAT PM DRIVE TRAIN SOLUTIONS ARE COMPACT, WITH LESS WEIGHT AND VOLUME THAN CONVENTIONAL DRIVE TRAINS
A TYPICAL PERMANENT MAGNET DRIVE TRAIN FROM THE SWITCH
THE SWITCH PMM 1000 M SHAFT GENERATOR
THE SWITCH ARGUMENT IS THAT PM DRIVE TRAIN SOLUTIONS ARE COMPACT, WITH LESS WEIGHT AND VOLUME THAN CONVENTIONAL DRIVE TRAINS
25 Mar 2015
According to Finland- based propulsion specialist, The Switch, permanent magnet (PM) drive train technology for electric propulsion brings a powerful solution to the big diesel dilemma, which combines tougher environmental considerations with a long-term perspective of increasing fuel costs.
PM machines could offer special seafaring vessels the opportunity to lower operational costs by optimising the fuel consumption of the diesel engine. Using permanent magnet (PM) motors and generators as key elements in advanced drive trains allows ship owners to take advantage of a more flexible, modular, efficient and lightweight propulsion system.
OPTIMAL PERFORMANCE
According to The Switch, PM drive trains are ideal for the electric propulsion of tugboats, OSVs, ferries, cruise lines, research vessels, icebreakers and more. The technology enables ships to lower their operational costs by optimising fuel consumption of the diesel engine. It is also known for its unmatched design flexibility. Thanks to their higher power density, PM machines can pack more power in a package that is far more compact, lighter in weight and smaller in size compared with induction machines.
PM machines have proven their high reliability and durability under extremely harsh operating conditions in many industrial applications. For example, they are used in wind turbines, which operate in a much harsher environment than the challenging marine market. In direct propulsion systems, no gearbox or accompanying slip rings and brushes are needed, as with other synchronous machines. Therefore, the PM propulsion machine experiences fewer failures and requires significantly less maintenance.
SYSTEM EFFICIENCY
The company also claims that a PM machine gives high-efficiency performance over the entire operating range, significantly cutting back on fuel consumption. The Switch’s figures claim that a PM machine is typically 2–4% more efficient at full load and 10% more efficient at part load when compared with induction machines. These efficiencies result from a lack of current losses in the rotor, the absence of an exciter, and reduced winding losses.
PM propulsion motors and their inverters efficiently turn available energy into thrust. Although standard induction motors can reach high efficiency in a narrow band around their nominal working area, PM motors are designed to deliver even higher efficiency in a much wider speed and torque range.
A synchronous PM machine contains Neodymium-Iron-Boron (NdFeB) magnets, which are materials with a very high flux density. This makes them ideal for variable-speed motors and generators throughout the entire speed range. The magnet field is created with almost zero rotor losses.
DYNAMIC POSITIONING
The electric propulsion of PM drive trains allows for extra maneuverability for dynamic positioning, which makes it a ideal technology for support and service ships like supply vessels, cruise ships or ice breakers. During dynamic positioning, a low speed with constant acceleration and deceleration is needed to keep the ship in place when adapting to weather and sea conditions. PM machines have the ability to function efficiently at low speeds and throughout the entire load range. In vessels where all energy is produced by fuel, a lower consumption leads to an improved operational range and lower operational costs.
Constantly varying speeds and loads can benefit from the active motor cooling, which keeps operating temperatures low. This results in small, but significant, efficiency improvements over time.
FREEQUENCY CONVERTORS
Optimised for best efficiency, the frequency converter is based on insulated gate bipolar transistors (IGBT) with advanced vector control technology. It is optimized to work with PM machines for the best overall system efficiency. The Switch frequency converters offer a modular, lightweight design, which enables efficient use of space within the vessel.
A frequency converter offers the accurate and adjustable speed control needed for dynamic positioning and demanding load cycles in offshore and special vessels. The high-energy density of PM technology and the resulting decrease in rotor inertia are both beneficial when the ship needs high maneuverability and a DP-class propulsion system. This results in optimum fuel efficiency and lower levels of exhaust.
To handle highly fluctuating load cycles, guarantee longer engine life, cut back on fuel consumption and reach lower exhaust values, adjustable speed control is ideal. This avoids the low or no-load running of generators, which minimises engine heat stress, reduces fuel consumption and eliminates undesired start/stop engine cycles.
TRACK RECORD
Although new to marine applications, The Switch adds that PM technology has in fact been a game changer for many years in other industries, such as wind power, where it ensures the highest energy efficiency and lowest cost of operation. As a bonus, this technology helps future-proof ships when it comes to even the strictest environmental legislation.
PM machines have a proven track record of efficiency and environmental friendliness in many demanding industrial applications, including marine, and according to The Switch they far outperform induction machines. Not only have PM drive trains shown that they lower fuel consumption and provide more power, but they are also proven to last longer and require less maintenance. Additionally, the compactness of PM drive trains leads to significant weight and space savings.
As cost pressures mount and environmental regulations become more stringent, multipurpose service vessels that operate primarily at partial load conditions need a novel approach to save on operational costs. The Switch argument is that PM drive train solutions are compact, with less weight and volume than conventional drive trains. They offer unsurpassed flexibility and a smaller footprint for all types of configurations, a huge advantage in the shipping environment where space is always a critical factor.
I have no doubt it will find application in Submarine propulsion in conjunction with IEPS specially in submarine where space is at premium and having high efficiency over large load range is premium in Sub operation resulting in longer range specially if diesel fueled
PM machines have the ability to function efficiently at low speeds and throughout the entire load range. In vessels where all energy is produced by fuel, a lower consumption leads to an improved operational range and lower operational costs.
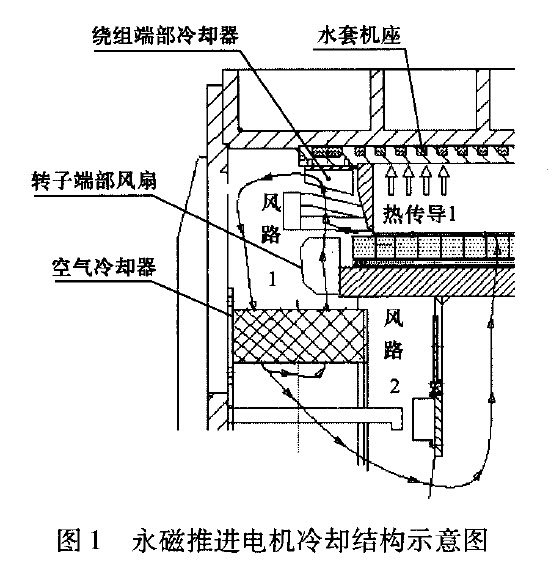
Here is the advantages of permanent motor over induction motor
PERMANENT MAGNET DRIVE TRAINS

THE SWITCH PMM 1000 M SHAFT GENERATOR

THE SWITCH ARGUMENT IS THAT PM DRIVE TRAIN SOLUTIONS ARE COMPACT, WITH LESS WEIGHT AND VOLUME THAN CONVENTIONAL DRIVE TRAINS

A TYPICAL PERMANENT MAGNET DRIVE TRAIN FROM THE SWITCH
THE SWITCH PMM 1000 M SHAFT GENERATOR
THE SWITCH ARGUMENT IS THAT PM DRIVE TRAIN SOLUTIONS ARE COMPACT, WITH LESS WEIGHT AND VOLUME THAN CONVENTIONAL DRIVE TRAINS
25 Mar 2015
According to Finland- based propulsion specialist, The Switch, permanent magnet (PM) drive train technology for electric propulsion brings a powerful solution to the big diesel dilemma, which combines tougher environmental considerations with a long-term perspective of increasing fuel costs.
PM machines could offer special seafaring vessels the opportunity to lower operational costs by optimising the fuel consumption of the diesel engine. Using permanent magnet (PM) motors and generators as key elements in advanced drive trains allows ship owners to take advantage of a more flexible, modular, efficient and lightweight propulsion system.
OPTIMAL PERFORMANCE
According to The Switch, PM drive trains are ideal for the electric propulsion of tugboats, OSVs, ferries, cruise lines, research vessels, icebreakers and more. The technology enables ships to lower their operational costs by optimising fuel consumption of the diesel engine. It is also known for its unmatched design flexibility. Thanks to their higher power density, PM machines can pack more power in a package that is far more compact, lighter in weight and smaller in size compared with induction machines.
PM machines have proven their high reliability and durability under extremely harsh operating conditions in many industrial applications. For example, they are used in wind turbines, which operate in a much harsher environment than the challenging marine market. In direct propulsion systems, no gearbox or accompanying slip rings and brushes are needed, as with other synchronous machines. Therefore, the PM propulsion machine experiences fewer failures and requires significantly less maintenance.
SYSTEM EFFICIENCY
The company also claims that a PM machine gives high-efficiency performance over the entire operating range, significantly cutting back on fuel consumption. The Switch’s figures claim that a PM machine is typically 2–4% more efficient at full load and 10% more efficient at part load when compared with induction machines. These efficiencies result from a lack of current losses in the rotor, the absence of an exciter, and reduced winding losses.
PM propulsion motors and their inverters efficiently turn available energy into thrust. Although standard induction motors can reach high efficiency in a narrow band around their nominal working area, PM motors are designed to deliver even higher efficiency in a much wider speed and torque range.
A synchronous PM machine contains Neodymium-Iron-Boron (NdFeB) magnets, which are materials with a very high flux density. This makes them ideal for variable-speed motors and generators throughout the entire speed range. The magnet field is created with almost zero rotor losses.
DYNAMIC POSITIONING
The electric propulsion of PM drive trains allows for extra maneuverability for dynamic positioning, which makes it a ideal technology for support and service ships like supply vessels, cruise ships or ice breakers. During dynamic positioning, a low speed with constant acceleration and deceleration is needed to keep the ship in place when adapting to weather and sea conditions. PM machines have the ability to function efficiently at low speeds and throughout the entire load range. In vessels where all energy is produced by fuel, a lower consumption leads to an improved operational range and lower operational costs.
Constantly varying speeds and loads can benefit from the active motor cooling, which keeps operating temperatures low. This results in small, but significant, efficiency improvements over time.
FREEQUENCY CONVERTORS
Optimised for best efficiency, the frequency converter is based on insulated gate bipolar transistors (IGBT) with advanced vector control technology. It is optimized to work with PM machines for the best overall system efficiency. The Switch frequency converters offer a modular, lightweight design, which enables efficient use of space within the vessel.
A frequency converter offers the accurate and adjustable speed control needed for dynamic positioning and demanding load cycles in offshore and special vessels. The high-energy density of PM technology and the resulting decrease in rotor inertia are both beneficial when the ship needs high maneuverability and a DP-class propulsion system. This results in optimum fuel efficiency and lower levels of exhaust.
To handle highly fluctuating load cycles, guarantee longer engine life, cut back on fuel consumption and reach lower exhaust values, adjustable speed control is ideal. This avoids the low or no-load running of generators, which minimises engine heat stress, reduces fuel consumption and eliminates undesired start/stop engine cycles.
TRACK RECORD
Although new to marine applications, The Switch adds that PM technology has in fact been a game changer for many years in other industries, such as wind power, where it ensures the highest energy efficiency and lowest cost of operation. As a bonus, this technology helps future-proof ships when it comes to even the strictest environmental legislation.
PM machines have a proven track record of efficiency and environmental friendliness in many demanding industrial applications, including marine, and according to The Switch they far outperform induction machines. Not only have PM drive trains shown that they lower fuel consumption and provide more power, but they are also proven to last longer and require less maintenance. Additionally, the compactness of PM drive trains leads to significant weight and space savings.
As cost pressures mount and environmental regulations become more stringent, multipurpose service vessels that operate primarily at partial load conditions need a novel approach to save on operational costs. The Switch argument is that PM drive train solutions are compact, with less weight and volume than conventional drive trains. They offer unsurpassed flexibility and a smaller footprint for all types of configurations, a huge advantage in the shipping environment where space is always a critical factor.
Last edited: