Progress in research on large-aperture grating diffraction wavefront control.
The research team of Bayinhexige and Li Wenhao from the National Grating Manufacturing and Application Engineering Technology Research Center of the Changchun Institute of Optics, Fine Mechanics and Physics, Chinese Academy of Sciences has made progress in the control of large-aperture grating diffraction wavefront.
Diffraction gratings can separate complex colors of light through periodic structures, and therefore are widely used in spectral analysis and wavefront control. The diffraction wavefront error will cause the performance of high-end instruments and equipment to deteriorate. In inertial confinement nuclear fusion, the grating diffraction wavefront error causes the laser beam combination wavefront distortion, affecting the quality of ultra-intense pulsed lasers; in astronomical spectrometers, the grating diffraction wavefront error will reduce the spectral resolution and detection sensitivity; in CNC machine tool displacement measurement systems, the grating diffraction wavefront error directly affects the displacement measurement accuracy. Therefore, the high-precision control of large-aperture grating diffraction wavefronts has become a core problem restricting the development of high-end instruments and equipment.
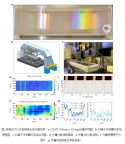
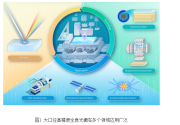
The outstanding advantage of the scanning interference field exposure technology is that the phase of the interference fringe can be actively controlled in real time, and a grating with extremely small diffraction wavefront error can be produced. The principle is that two laser beams are superimposed at their beam waists to form a millimeter-diameter interference field on the grating surface, and the workbench performs two-dimensional step scanning motion for exposure. Therefore, the accuracy of the workbench displacement measurement directly determines the accuracy of the grating diffraction wavefront. However, traditional laser interferometry is easily affected by ambient temperature, humidity and pressure, and the displacement measurement accuracy of the workbench is reduced. To solve the above problems, the research team proposed a grating-laser complementary workbench displacement measurement technology, which uses a grating interferometer that is less affected by environmental factors at the far end for long-distance measurement, and a laser interferometer for short-distance measurement at the near end, thereby solving the contradiction between the range and accuracy of the workbench displacement measurement, and the repeatability accuracy of the workbench measurement reaches ±6nm. The research team also established a nanometer-precision interference field parameter measurement system. Through two sets of measurement systems, the displacement error of the workbench and the phase distribution of the exposure beam can be accurately obtained, and the dynamic phase control system is used to modulate the phase distribution of the interference fringes to achieve accurate phase splicing of adjacent interference fringes. This method can compensate for the grating line error caused by the worktable motion error and achieve high-precision production of large-aperture gratings.